Innovation & Performance: New cutting chamber design
CMG is introducing a brand new cutting chamber design for its Evoluzione series granulators. The new rotor configuration allows the rotor blades to cut the plastic feedstock perpendicularly against the bed blades, obtaining the highest degree of cutting penetration and precision.
The rotor blades are mounted on the edge of the rotor holding modules and not on a holding block. Not only this feature is beneficial, as the inclination of the rotor blades is very high, but it also allows easy and quick servicing/replacement of the blades, with comfortable access from the front of the machine.
The rotation of the rotor does not produce the very detrimental “drag” effect, meaning the mass of material being ground in the cutting chamber does not rotate with the rotor producing lots of dust and fine particles, that will all become waste through the washing line. The production of fine particles is reduced to few percentage points, versus a common 15% or more from conventional granulators.
The rotor is of the open type design, taking only 30% of the cutting chamber volume.
The rotor/cutting chamber volume utilization ratio is 30/70, versus alternative ordinary granulators with 70/30 ratio. This feature alone allows more than double the quantity of material in the cutting chamber. The more is the material in the cutting chamber, the higher is the capacity of granulation.
The new cutting chamber has the so called “tangential set up”. Such characteristic confers voraciousness and guaranteed bite, with no need of feeding aid devices, commonly utilized with conventional granulators.
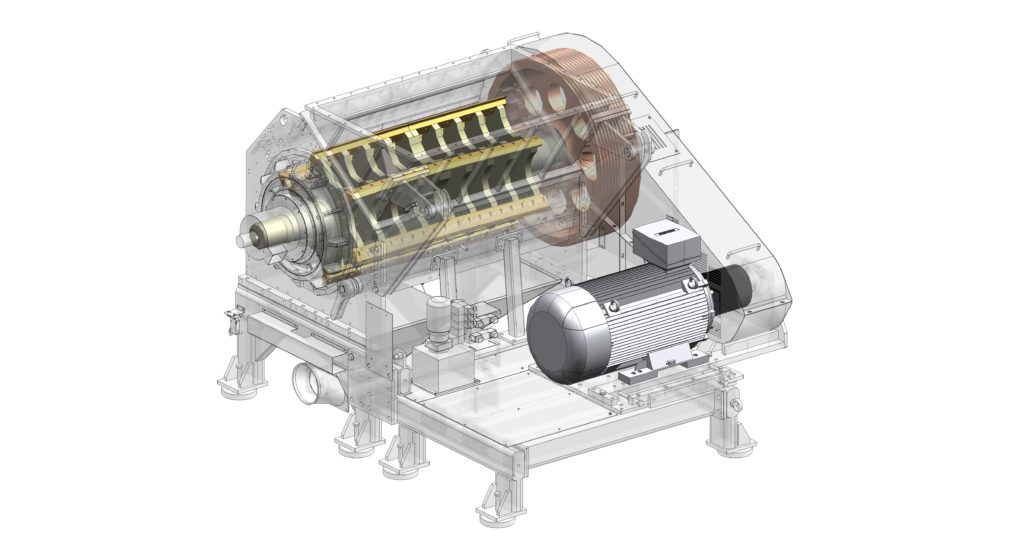
Energy efficiency at the highest level: Adaptive Motor Power
All CMG units for Recycling applications, with capacities from 800 kg/h to over 5,000 kg/h, feature the Adaptive Motor Power (AMP) function, unique in the size reduction industry. The granulator is able to autonomously establish which power level to adopt to carry out its work, according to quantity of material to be ground, shape, weight, thickness, type of plastic, and temperature of the piece. The AMP allows to optimize the quality of the regrind material to the maximum (dimensional and physical homogeneity of the regrind particle and absence of dust) and minimize the use of electricity. From 20 to 25 Wh/kg is the small amount of energy that a CMG granulator uses, compared to over 50 Wh/kg that a conventional unit consumes. The ROI for the AMP is less than 12 months.
Super granulators for post-consumer recycling
With the new Evoluzione series, CMG presents the EV916 and EV616 models, solutions suitable for the most critical operating conditions, for wet or dry granulation, which require high performance characteristics such as granulation capacity from 2,000 to over 5,000 kg/h, versatility, efficiency and sustainability. The Evoluzione series guarantees operational consistency and wear resistance of a higher degree, with its construction solutions that involve the use of harmonic steel, Hardox and assembled modular structures. In addition to the precision to the hundredth of a millimeter on the construction of the new cutting chamber, which allows a much longer duration of the blades when compared to conventional models, all the Evoluzione are equipped with advanced controls, in the Industry 4.0 style, to make the machine functions 100% monitorable and manageable. Operating temperature, blade wear, productivity, operational efficiency, energy use, all functional parameters managed on the machine or remotely, with connectivity based on the OPC-UA protocol, are just some distinctive features.
Service 4.0:
With Headquarters, Production Site and Technical Center in Italy, and the largest distribution network in the plastics industry, CMG is active all over the world with localized technical service, spare parts and sales centers. Find the nearest CMG service center at the following link https://www.cmg-granulators.com/en/contacts-3/